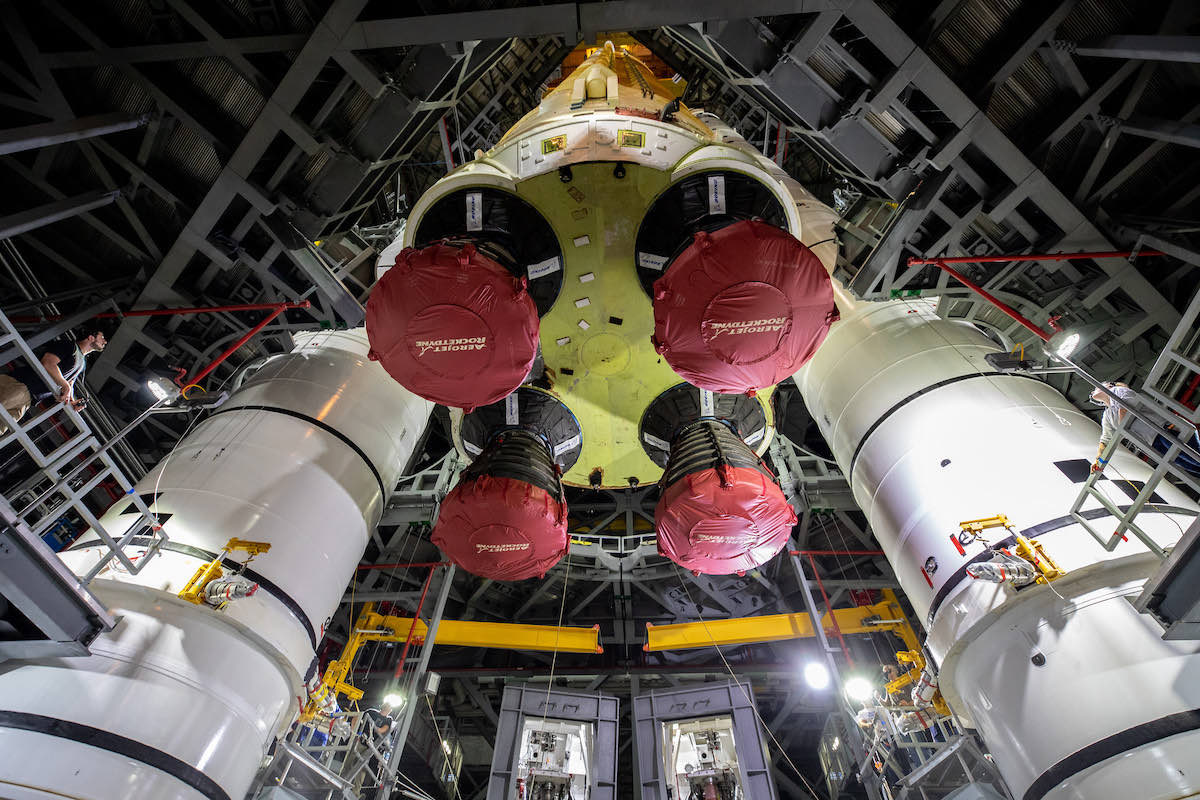
The core stage for NASA’s first Space Launch System, the heavy-lift rocket designed to carry astronauts back to the moon, has been installed between two solid-fueled boosters on a mobile launch platform at the Kennedy Space Center for an unpiloted lunar test flight.
The 212-foot-tall (65-meter) orange core stage was raised vertical inside the Vehicle Assembly Building on June 11. A 325-ton crane hoisted the rocket several hundred feet above the floor of the huge assembly building June 12, then transferred the stage from the structure’s middle passageway, or transfer aisle, into an adjacent high bay.
The final stage of the around-the-clock, multi-day operation was to carefully lower the empty core stage in between the Space Launch System’s twin solid rocket boosters, which are already loaded with pre-packed solid propellants.
A NASA spokesperson said “soft mate” between the core stage and solid rocket boosters, longer versions of the solid-fueled motors used on the space shuttle, was completed in High Bay 3 of the Vehicle Assembly Building around 10 p.m. EDT June 12 (0200 GMT June 13).
Officials declared “hard mate” complete at 7 a.m. EDT (1100 GMT) on Sunday, June 13, when technicians completed structural connections at attach points at the forward and aft ends of the core stage, which weighs about 94 tons (85 metric tons) empty.
With the rocket components firmly mated, the crane disconnected from the core stage, leaving the two 177-foot-tall (54-meter) solid rocket boosters to carry the full weight of the rocket. The SLS main stage is suspended between the Northrop Grumman-made boosters, which are stacked on mounting pins on the mobile launch platform.
Unlike the space shuttle, there are no hold-down bolts connecting the solid rocket boosters to the mobile launch platform, which was designed specifically for the Space Launch System.
Four support posts, fitted with strain gauges to measure loads during stacking, rollout, and launch, serve as structural mounting points for each booster on the deck of the mobile platform.
The core of NASA’s first Space Launch System, the heavy-lift rocket designed to carry astronauts back to the moon, has been bolted between two solid-fueled boosters on a mobile launch platform at the Kennedy Space Center for an unpiloted lunar test flight. https://t.co/NJytqOh0Ae pic.twitter.com/gJRcJ9A3vC
— Spaceflight Now (@SpaceflightNow) June 17, 2021
The stacking of the core stage begins a process that NASA officials say should culminate in a fully-assembled Space Launch System and Orion spacecraft as soon as August. If everything goes on a schedule, a major “if” for a brand new rocket with a history of delays, NASA could move the 322-foot-tall (98-meter) rocket to pad 39B on top of one its giant Apollo-era crawler-transporters in September or October for a mock countdown and fueling test.
NASA hopes to launch the SLS and Orion crew capsule on an unpiloted test flight around the moon as soon as late November. The mission, known as Artemis 1, will last more than three weeks and pave the way for the next SLS/Orion mission, Artemis 2, to carry a four-person crew around the moon in 2023.
Artemis missions later in the 2020s will land astronauts near the south pole of the moon using commercially-developed lunar landers. In April, NASA selected a variant of SpaceX’s Starship, a reusable heavy-lift rocket being developed with majority private funding, to land the first Artemis crew on the moon.
But NASA plans to use the government-owned Space Launch System rocket and Orion capsule for the round-trip flight between Earth and the vicinity of the moon, where astronauts will transfer into a lunar lander, such as the Starship, for descent to the surface.
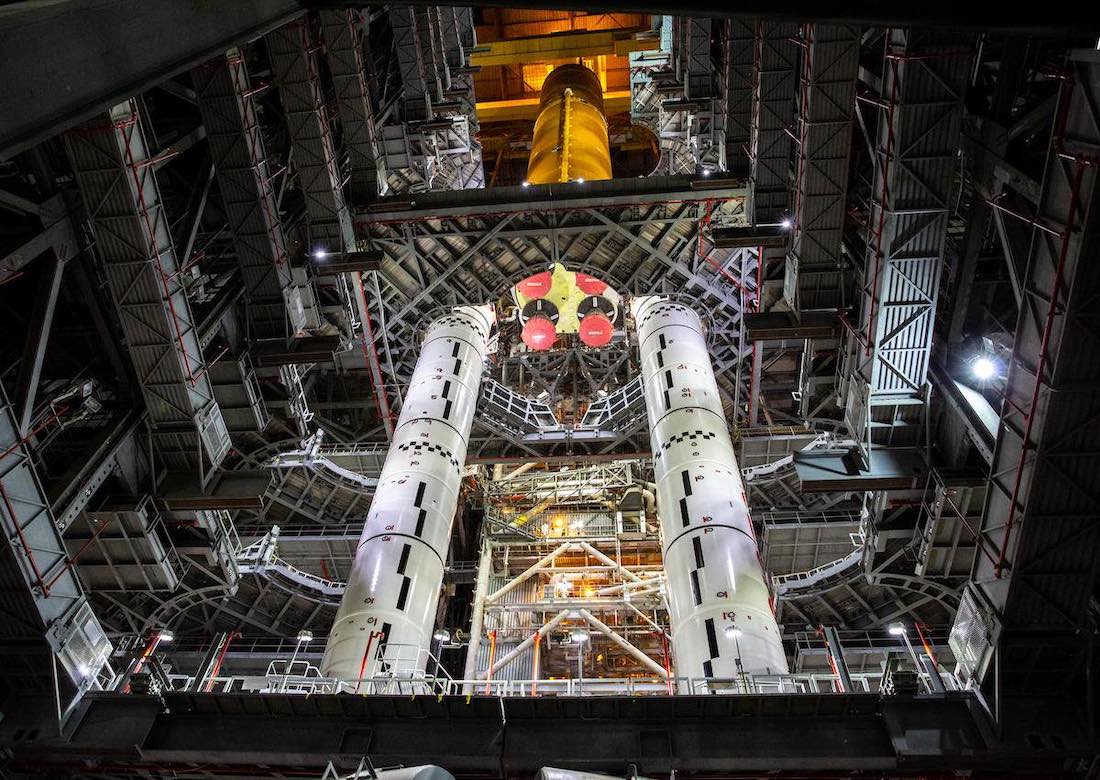
During launch, the core stage’s Aerojet Rocketdyne RS-25 engines and twin solid rocket boosters will generate 8.8 million pounds of thrust. It can send about 59,500 pounds (27 metric tons) of payload to the moon, more than any rocket operating today.
The ground crew inside the VAB rehearsed the lift and mate procedures in 2019 with a pathfinder structure built to mimic the weight and size of the SLS core stage. Before the SLS boosters were stacked a few months ago, the last time the VAB cranes lifted real rocket hardware in preparation for launch was before the final space shuttle mission in 2011.
The hoisting of the SLS core stage comes about six weeks after the rocket rolled into the Vehicle Assembly Building at Kennedy, following an ocean journey aboard a NASA barge from the Stennis Space Center in Mississippi. Ground crews at Stennis test-fired the rocket’s four RS-25 engines for more than eight minutes in March to simulate a full launch profile.
Since the core stage arrived in Florida in late April, teams from NASA and Boeing, the rocket’s prime contractor, repaired dozens of areas of orange foam thermal insulation damaged during the eight-minute test-firing at Stennis. They also touched up cork thermal insulation on the bottom of the rocket’s engine section that charred during the hotfire test earlier this year.
The foam helps regulate temperatures inside the main stage’s cryogenic propellant tanks, which will hold more than 730,000 gallons of liquid hydrogen stored at minus 423 degrees Fahrenheit (minus 253 degrees Celsius) and liquid oxygen at minus 298 degrees Fahrenheit (minus 183 degrees Celsius).
Engineers also identified a few sensors that needed repair on the outside of the rocket. A small fraction of the more than 500 sensors designed to collect data the rocket’s performance and environments debonded during the test-firing.
And ground crews finished installing linear shaped charges along the core stage’s exterior. The charges are part of the flight termination system, which would destroy the rocket if it flew off course and threatened the public.
With the core stage in place, the pace of stacking will be be “fairly quick,” said Cliff Lanham, senior vehicle operations manager for NASA’s exploration ground systems program.
Next will be the Launch Vehicle Stage Adapter, or LVSA, the interstage structure that will connect the main stage with the rocket’s upper stage.
The LVSA is scheduled to be installed on top of the core stage this week.
Then the Interim Cryogenic Propulsion System, or ICPS, will be added to the Space Launch System as soon next week in High Bay 3. The hydrogen-fueled upper stage is derived from the second stage of United Launch Alliance’s Delta 4-Heavy rocket.
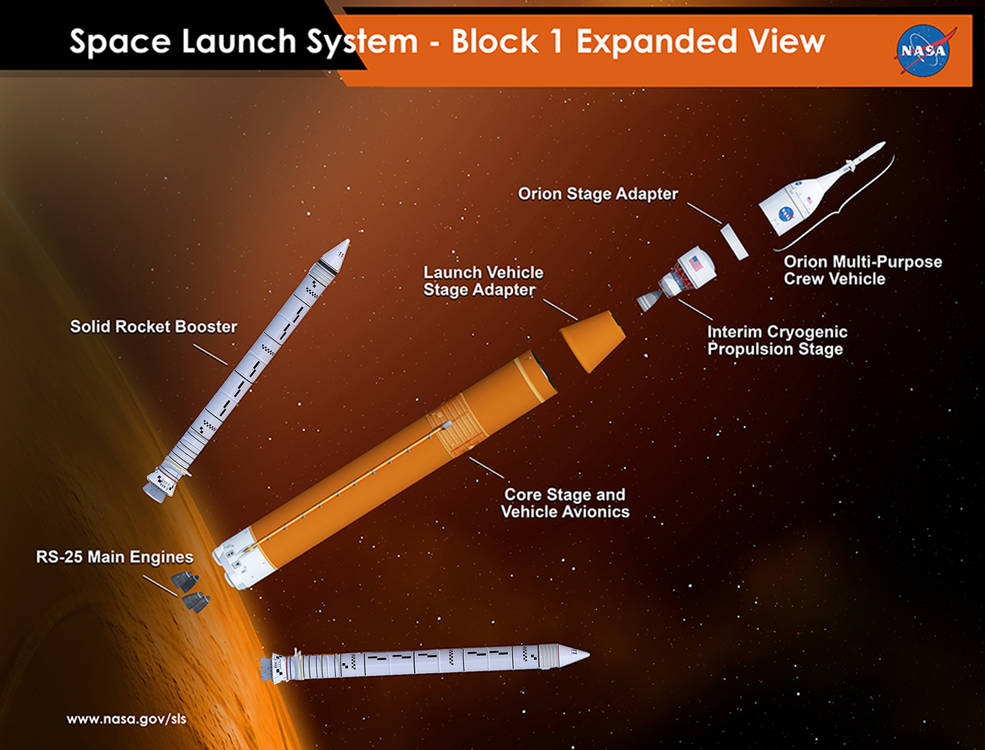
The upper stage is currently being readied for launch inside the Multi-Payload Processing Facility at Kennedy. When teams in High Bay 3 are ready, the ICPS will ride on a transporter several miles to the VAB to be raised atop the Space Launch System.
“It’s a pretty aggressive stacking sequence that we’ll be following, all in an effort to get us ready and get the umbilicals mated so we can get into our power up and get into our real big test, which will be our umbilical retract test,” Lanham said in a recent interview.
Once the upper stage is installed, ground teams will lift another adapter designed to connect the Orion capsule. Then a structure will go on top of the rocket to simulate the weight of the Orion spacecraft.
That will set the stage for a test to verify the propellant lines, fluid connections, and other umbilicals running between the mobile launch platform’s tower and the rocket can safely release and retract as they will at liftoff.
Then teams will move into structural resonance testing, or modal testing, of the fully-stacked launch vehicle in July. Once that is complete, teams will move the real Orion spacecraft — which will already be integrated with its launch abort system — to the VAB for attachment to the top of the Space Launch System, an event that could happen as soon as early August, Lanham said.
After the practice countdown, which NASA calls a wet dress rehearsal, the SLS and Orion spacecraft will return to the Vehicle Assembly Building for final closeouts, inspections, and ordnance connections.
The next time the rocket rolls out to pad 39B will be around six day before launch, Lanham said.
“We’ll face challenges ahead, he said. “We’re heading into hurricane season. We’ll see how that plays out. It’s the first time we’ve done this, so we’ll run into issues there, but we are absolutely trying to get this launched by the end of the year.”
Email the author.
Follow Stephen Clark on Twitter: @StephenClark1.